Weather-proof Actuator


Directly used outdoors without additional protection
Applicable for part-turn Valve
IP68
Movement Direction
Part-turn
Damper
0 - 90° | 0 - 360°
Torque/Operating Time
20 - 2500Nm
4S - 75S
Type of Duty
Modulating
Inching - Positioning
On - Off
Supply Voltage
DC24V
AC24V
AC110V
AC220V
AC380V
Input/Output Signal
4~20mA
0~10V
IO Interface
Operational with fieldbus
Modbus-RTU
Modbus-ASCII
CAN
Ethernet
Additional Options
Over-torque Protection
Fail Safe Return
Dehumidification
Diagnosis
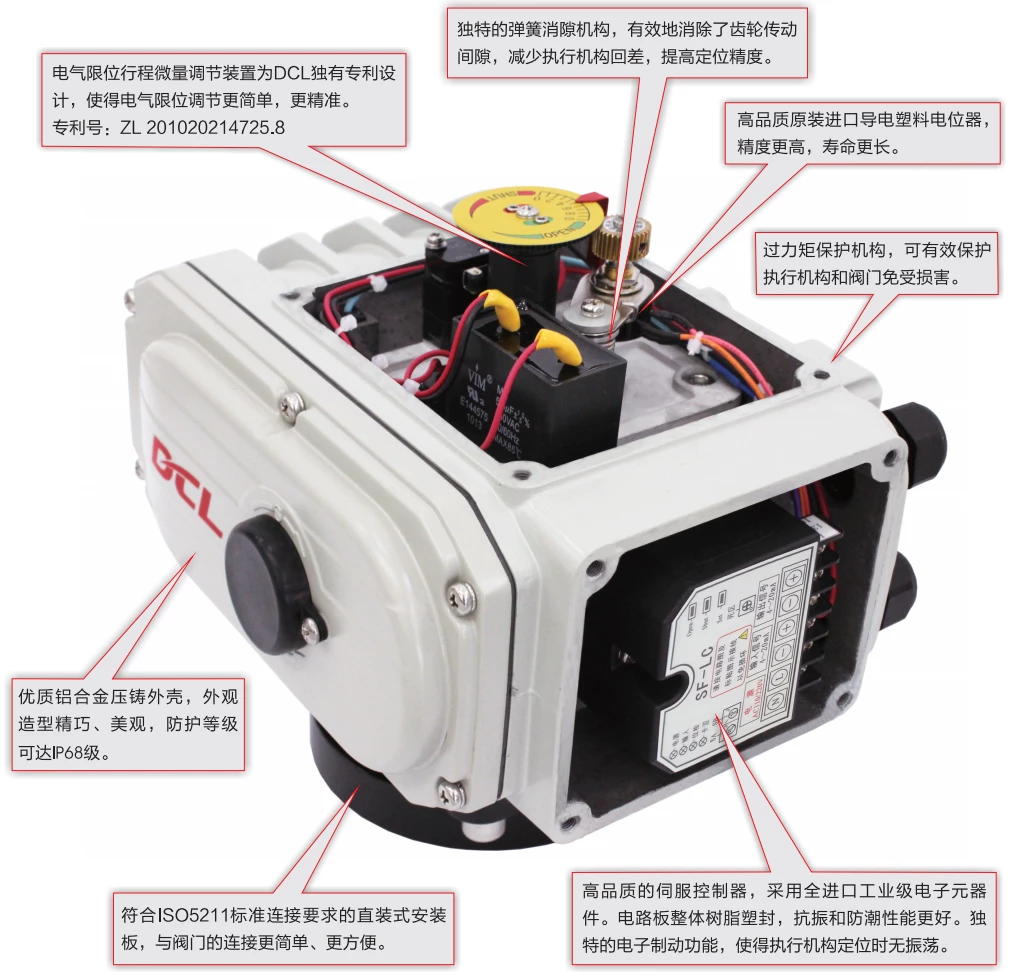
Type of Duty
Modulating
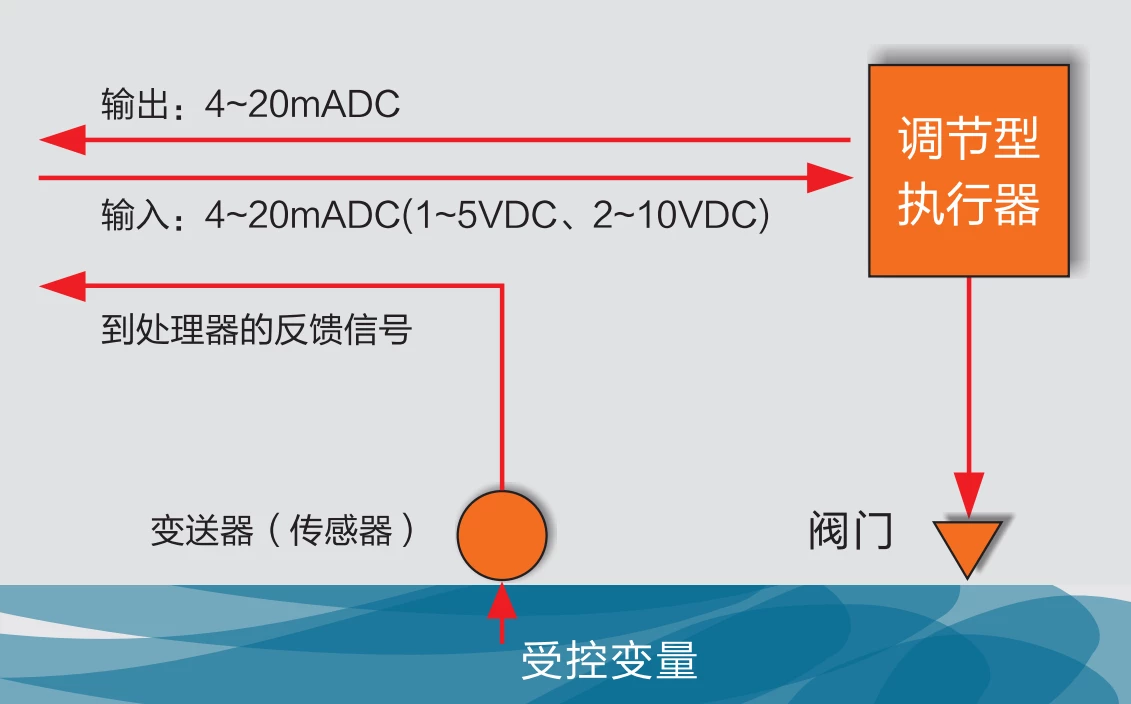
The actuator read the target position value from control system through 4-20mA, 2-10V or field bus such as modbus, ethernet and etc.
Then actuator drive the valve to the target position with interior control algorithm.
The actuator will always output the real-time valve position through 4-20mA, 2-10V or field bus.
Operated in type of duty S4, the actuator can starts 1200 times per hour.
On - Off
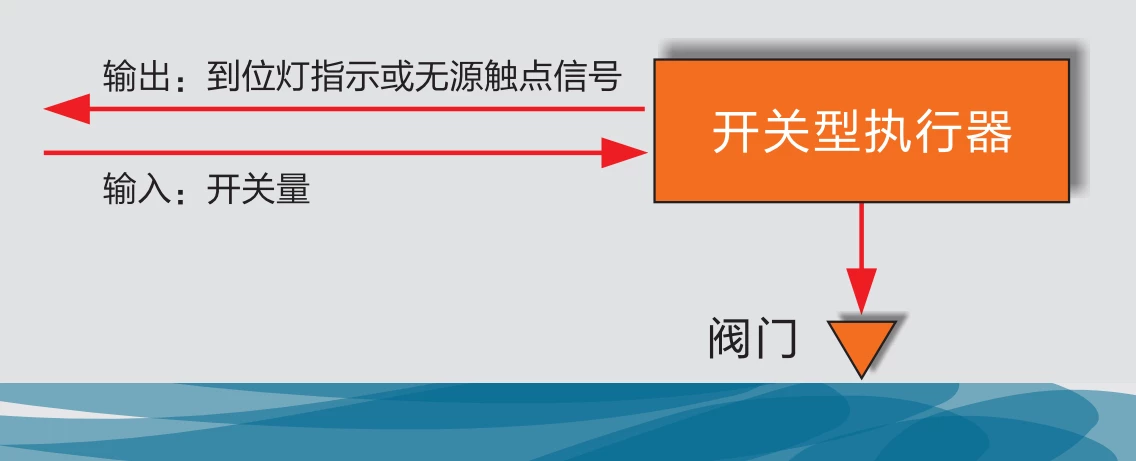
The actuator read the open or close requirement from control system through IO interface such as passive signal or 24VDC/220VAC active signal.
Then actuator drive the valve to the end-position of OPEN or CLOSE as input signal required.
The actuator will output a feedback signal of OPEN or CLOSE when end-position been reached.
Operated in type of duty S2, the actuator can drive valve continuously for 15 minutes.
Inching - Positioning
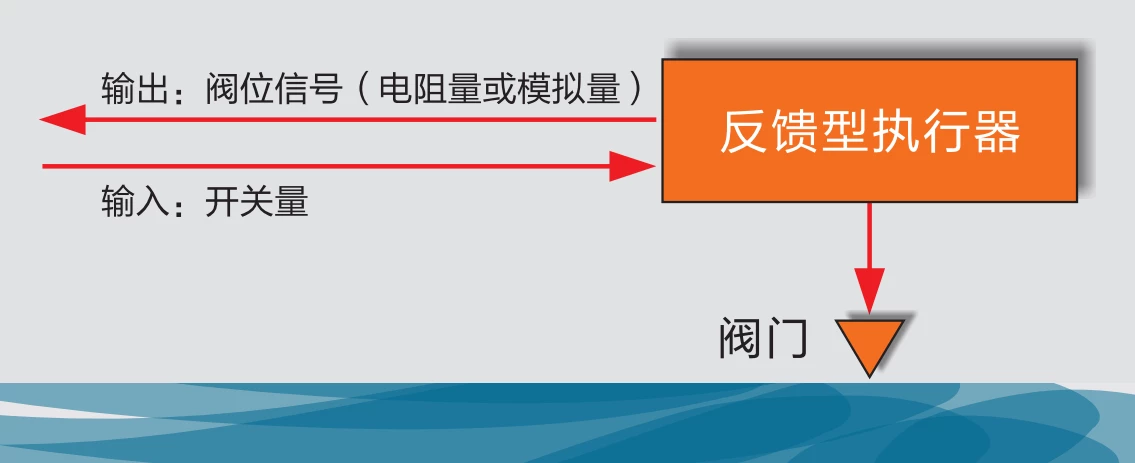
The actuator read the inching OPEN or CLOSE signal from control system through IO interface inputted with 24VDC/220VAC active signal.
Then actuator drive the valve with a stepping way specified by the input inching signal.
The actuator will always output the real-time valve position as a potentiometer resistance value or 4-20mA/2-10V value.
Operated in type of duty S2, the actuator can drive valve continuously for 15 minutes.
Features
Fully Capsulated Control Unit
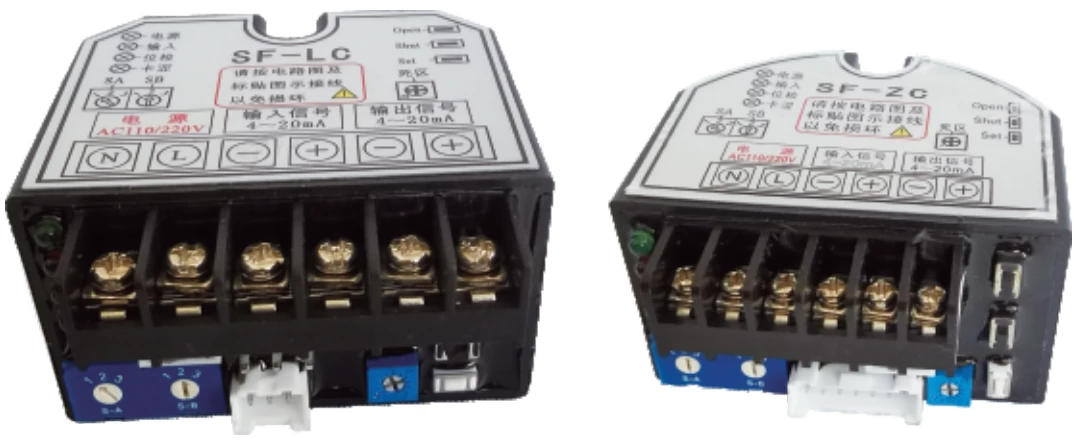
The control unit is fully encapsulated with polyurethane. This greatly enhanced proof performance against moisture, condensation, salt and vibration. So it is applicable in harsh environments such as high humidity, dust, strong temperature changing, vibration, etc.
With 6kV EFT and surge protection circuit, the stable control to the valve can be ensured even in worst electromagnetic environment.
By self-adjustment algorithm, the actuator can keep the precision against different loads conditions and mechanical wear by time.
Easy-to-use Limit Switch
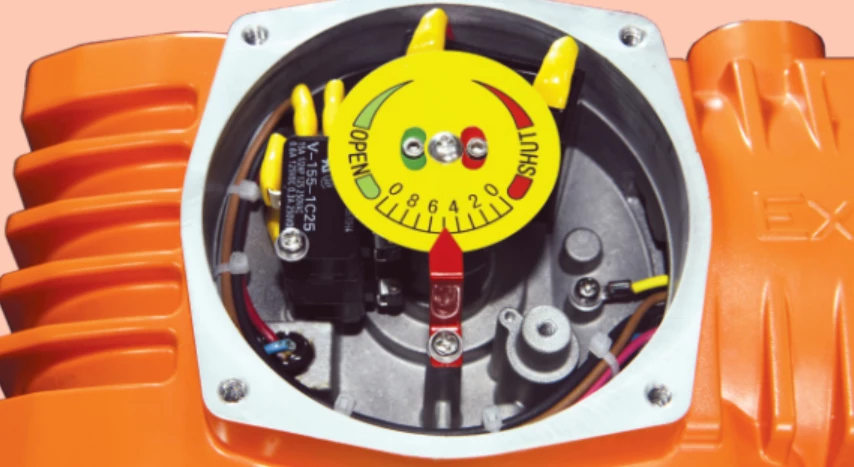
With DCL’s patented limit switch design, the actuator’s end position of open and close can be easily configured only with a hexagonal wrench.
In the meantime the micro adjustment feature of limit switch can improve the precision when setting the end-position.
Patent No. ZL 201020214725.8
Motor with Over Temperature Protection
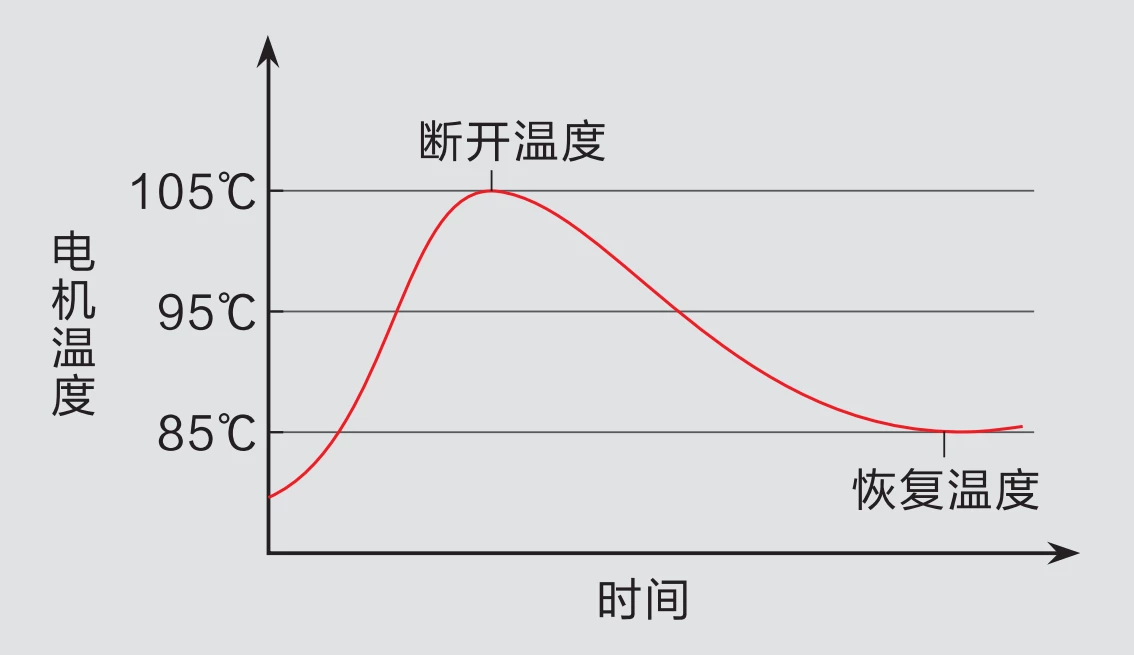
DCL specially design the motor to fit the actuator requirement so that the motor in DCL actuator can supply a high start torque while maintain a high efficiency in the start phase to make the temperature rise as low as possible. In the meantime the motor have a small moment of inertia to make sure the high precision in modulation.
There is an over temperature protection device mounted in the motor which will cut the power supply when the motor temperature goes higher then the limited temperature(105℃/85℃ can be selected up on the application scenario) and connect the power supply again when the temperature recovered below the Normal temperature.
Dual Position Limiter
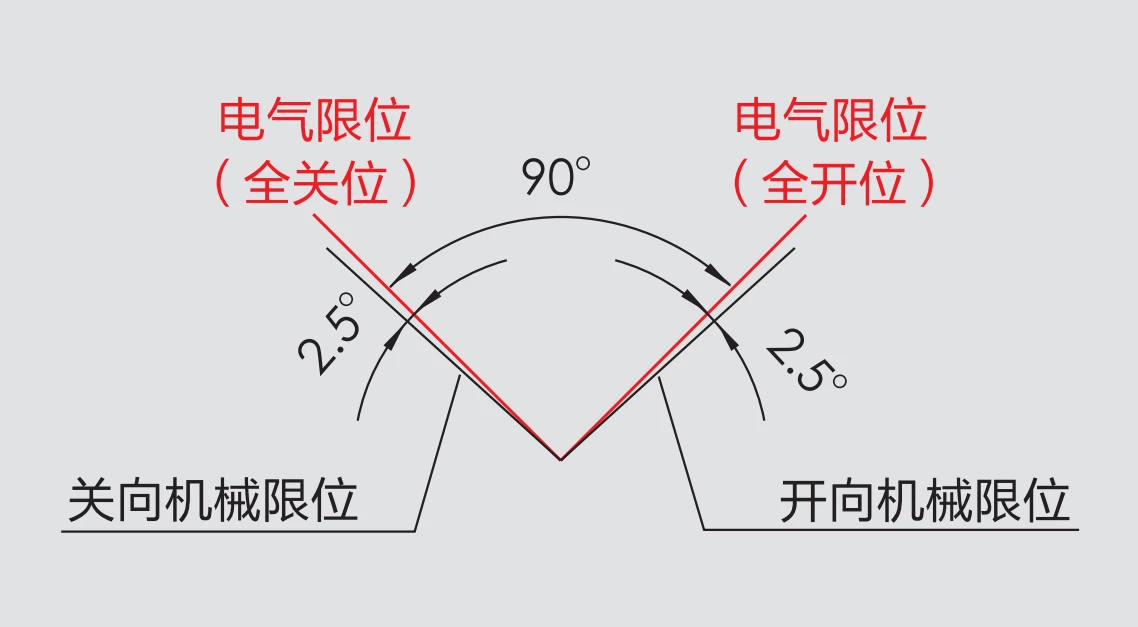
There are 2 position limit devices to protect valve from damage by operation over swing angle.
Electric limit switch are mounted on the both end-position of OPEN and CLOSE. So the power supply to motor will be cut off to stop driving the valve after limited end-position was reached.
Also there are 2 mechanical limiters mounted on the output shaft to protect the valve from swing over stroke range. The mechanical limiter will not take effect in normal operation cause the electric limit switch is ahead of the mechanical limiter and will be triggered before the output shaft can reach the mechanical limited positon.
Additional Options
Over-torque Protection
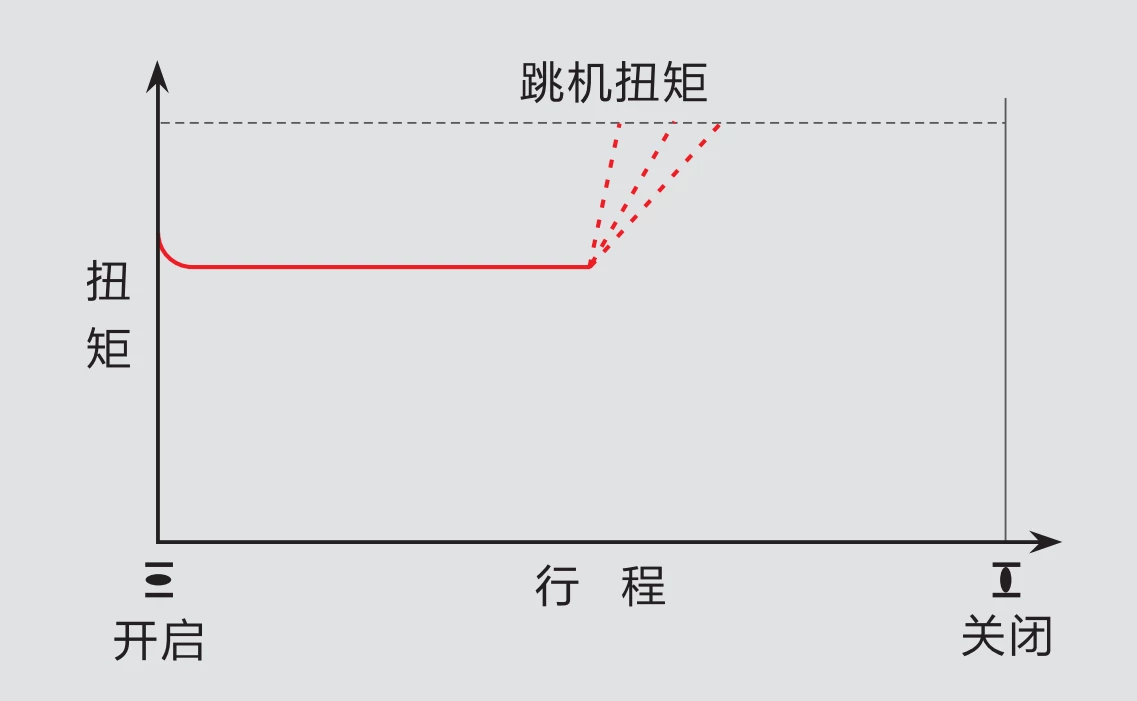
When the valve is stuck by some reason such as solid impurities in the liquid or malfunction on some mechanical parts, the torque on output shaft of actuator will increased sharply beyond the limit torque value when driving the valve, then the actuator would trig an over torque protection to stop driving the valve in order to protect the valve from damage.
Dehumidifying
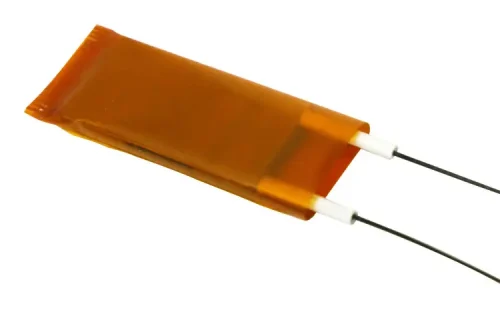
You can choose a dehumidifying option on DCL actuator. Then a electric PTC heater will be mounted in the actuator to reduce humidity to protect circuit from malfunction in high range of temperature changing circumstance due to condensation.
The PTC heater will be in working mode as long as power is supplied to actuator.
Circuit Diagram
Modulating
E - Modulating with a control unit
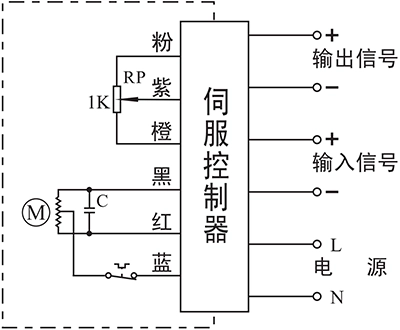
- Input: 4~20mA / 0~10V
- Output: 4~20mA / 0~10V
- Field Bus:Modbus / CAN
- IIot:WIFI/LoRA/4G DTU
Inching and positioning
F - With a positioning unit
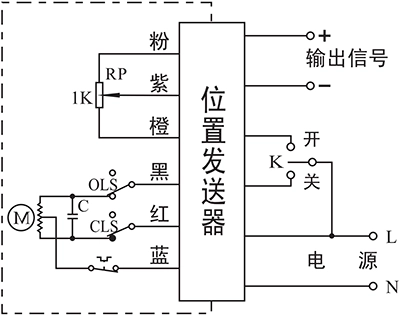
- Control actuator to open or close with K
- The real-time valve position will be send out as a 4-20mA signal
C - With a 1KΩ/500Ω potentiometer
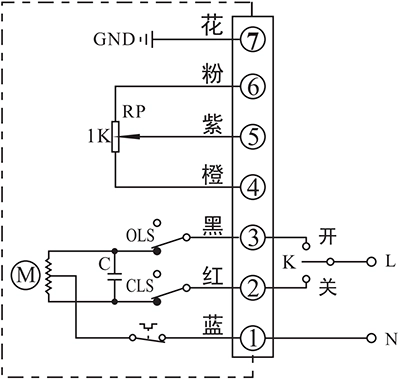
- Control actuator to open or close with K
- The real-time valve position will be send out as a potentiometer resistance value
D - With a potentiometer and end-position feedback
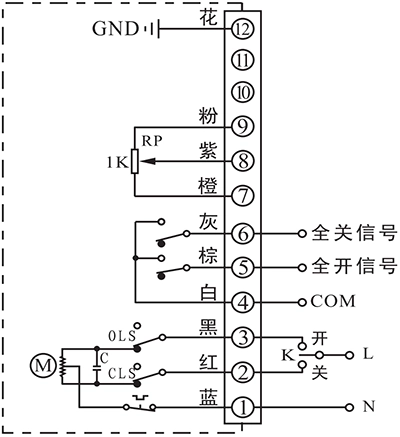
- Control actuator to open or close with K
- The real-time valve position will be send out as a potentiometer resistance value
- The output terminal of end-position OPEN/CLOSE will send out the event as a passive signal form when the end-position was reached.
ON - OFF
A - With 2 active end-position signal outputs
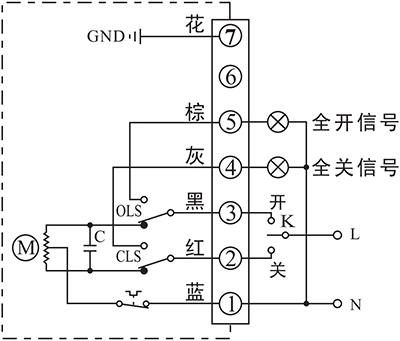
- Control actuator to open or close with K
- The output terminal of end-position OPEN/CLOSE will send out the event as a 220VAC active signal form when the end-position was reached.
B - With 2 passive end-position switches
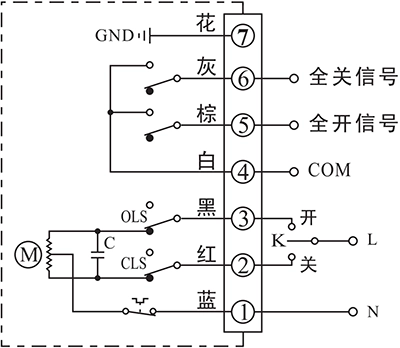
- Control actuator to open or close with K
- The output terminal of end-position OPEN/CLOSE will send out the event as a passive signal form when the end-position was reached.
G - DC motor with 2 end-position switches
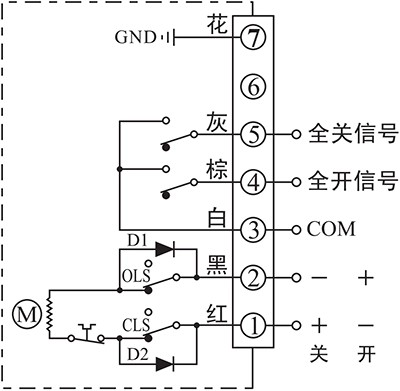
- Control actuator to open or close by the supply power direction between the terminal 1 and 2
- The output terminal of end-position OPEN/CLOSE will send out the event as a passive signal form when the end-position was reached.
H - 3 phase 380VAC motor with 2 end-position switches
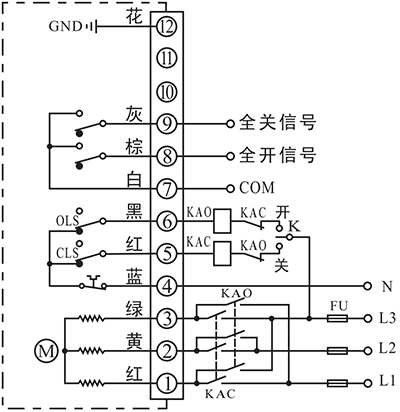
- Control actuator to open or close by an external inverter to change the phase of supply power.
- The output terminal of end-position OPEN/CLOSE will send out the event as a passive signal form when the end-position was reached.
Note:
- The circuit inside the dashed box is the internal circuit of actuator. While the circuit outside is a demonstration of electrical connection for using actuator.
- If you have other specific requirements about connecting circuit, please feel free to contact our technical support.
Basic Parameters
Model | Swing Angle | Torque/Operating Time | Duty Type | Supply Voltage | Input/Output Signal | Additional Options |
---|---|---|---|---|---|---|
DCL-05 | 0 - 360° | 50Nm/20s Optional with 20Nm/4s 30Nm/10s 50Nm/60s | ON - OFF Modulating Inching - Positioning | DC24V AC24V AC110V AC220V AC380V | 4-20mA 0-10V IO Interface Optional with field bus Modbus-RTU Modbus-ASCII CAN Ethernet | Over torque protection Fail Safe Return Dehumidification Field Bus |
DCL-10 | 0 - 360° | 100Nm/30s Optional with 20Nm/4s 30Nm/10s 50Nm/60s | ON - OFF Modulating Inching - Positioning | DC24V AC24V AC110V AC220V AC380V | 4-20mA 0-10V IO Interface Optional with field bus Modbus-RTU Modbus-ASCII CAN Ethernet | Over torque protection Fail Safe Return Dehumidification Field Bus |
DCL-20 | 0 - 90° | 200Nm/30s Optional with 100Nm/15s 200Nm/60s | ON - OFF Modulating Inching - Positioning | DC24V AC24V AC110V AC220V AC380V | 4-20mA 0-10V IO Interface Optional with field bus Modbus-RTU Modbus-ASCII CAN Ethernet | Over torque protection Fail Safe Return Dehumidification Field Bus |
DCL-40 | 0 - 90° | 400Nm/30s Optional with 200Nm/15s 400Nm/60s | ON - OFF Modulating Inching - Positioning | DC24V AC24V AC110V AC220V AC380V | 4-20mA 0-10V IO Interface Optional with field bus Modbus-RTU Modbus-ASCII CAN Ethernet | Over torque protection Fail Safe Return Dehumidification Field Bus |
DCL-60 | 0 - 90° | 600Nm/45s | ON - OFF Modulating Inching - Positioning | DC24V AC24V AC110V AC220V AC380V | 4-20mA 0-10V IO Interface Optional with field bus Modbus-RTU Modbus-ASCII CAN Ethernet | Over torque protection Fail Safe Return Dehumidification Field Bus |
DCL-100 | 0 - 90° | 1000Nm/30s Optional with 500Nm/15s | ON - OFF Modulating Inching - Positioning | AC110V AC220V AC380V | 4-20mA 0-10V IO Interface Optional with field bus Modbus-RTU Modbus-ASCII CAN Ethernet | Over torque protection Fail Safe Return Dehumidification Field Bus |
DCL-160 | 0 - 90° | 1600Nm/48s | ON - OFF Modulating Inching - Positioning | AC110V AC220V AC380V | 4-20mA 0-10V IO Interface Optional with field bus Modbus-RTU Modbus-ASCII CAN Ethernet | Over torque protection Fail Safe Return Dehumidification Field Bus |
DCL-250 | 0 - 90° | 2500Nm/75s | ON - OFF Modulating Inching - Positioning | AC110V AC220V AC380V | 4-20mA 0-10V IO Interface Optional with field bus Modbus-RTU Modbus-ASCII CAN Ethernet | Over torque protection Fail Safe Return Dehumidification Field Bus |
Recommend actuator to drive a butterfly valve
Recommend actuator to drive a Ball valve
Recommend actuator to drive a ventilation valve
Recommend valve to be driven by DCL weather-proof actuator
Model | Torque (Nm) | Butterfly Valve (≤ PN1.0MPa) | Ball Valve (≤ PN1.6MPa) | Ventilation Valve (≤ PN0.1MPa) |
---|---|---|---|---|
DCL-05 | 50 | DN50~65 | DN40 | DN50~80 |
DCL-10 | 100 | DN80~100 | DN50~65 | DN100~200 |
DCL-20 | 200 | DN125~150 | DN80~100 | DN250~300 |
DCL-40 | 400 | DN200 | DN125 | DN350~450 |
DCL-60 | 600 | DN250 | DN150 | DN500~600 |
DCL-100 | 1000 | DN300 | DN200 | DN700~800 |
DCL-160 | 1600 | DN350~400 | DN250 | DN900 |
DCL-250 | 2500 | DN450~600 | DN300~350 | DN1000~1200 |
Note: The recommendations in the above table is for reference only in common application scenario, the specific torque needed to drive the valve is depended up on the real application case.
It is recommended to choose an actuator with 1.1-1.3 times of torque than the value that was finalized after evaluation of torque requirement of valve and liquid pressure in the pipe. This would improve the robust performance in most worst case.
View actuators with different torque
50Nm/20S
————————–
Optional with
20Nm/4S
30Nm/10S
50Nm/60S
50Nm/100S